Landing Gear Kinematics Simulation with Laws – CATIA V5
Aafreen KaurProject Overview
This project involves designing and simulating a landing gear mechanism using CATIA V5, focusing on the kinematic behavior of components. The simulation is performed with defined motion laws to control the retraction and extension of the landing gear.
Components Used:
- Fuselage Fixed Part: The stationary reference part to which the landing gear is attached.
- Shock Strut: Absorbs impact forces during landing.
- Actuators & Pistons: Responsible for retracting and extending the landing gear.
- Oleo Strut: Provides additional damping and absorbs shocks.
- Trunnion: Acts as a pivot for the landing gear mechanism.
- Brace & Door Link: Supports and locks the gear in place.
- Tire and Axle Assembly: The main wheel system for landing and taxiing.
- Landing Gear Door: Protects the retracted landing gear and reduces aerodynamic drag.
Joints Used:
The kinematic model employs different joint types:
- Revolute Joints: Used between pivoting components (e.g., between the trunnion and fuselage, or the oleo strut and shock strut).
- Cylindrical Joints: Applied to allow linear and rotational movement (e.g., for actuators and pistons).
- Rigid Joints: Used where no relative motion occurs (e.g., fixing components together).
- Slide Joints: Used in doors to simulate movement along a path.
Simulation & Motion Laws:
- The motion is governed by laws defining displacement over time to achieve realistic extension and retraction.
- The commands panel in CATIA V5 is used to control the motion of:
- Landing Gear Movement
- Door Opening/Closing
- Shock Absorption and Actuation
- Kinematic Simulation Panel allows precise tuning of movement ranges and time-dependent changes.
Purpose & Applications:
This project helps in:
- Validating landing gear kinematics before physical manufacturing.
- Optimizing motion paths to prevent mechanical interference.
- Ensuring smooth and controlled extension/retraction for safety compliance.
- Providing insights for aircraft landing gear design improvements.
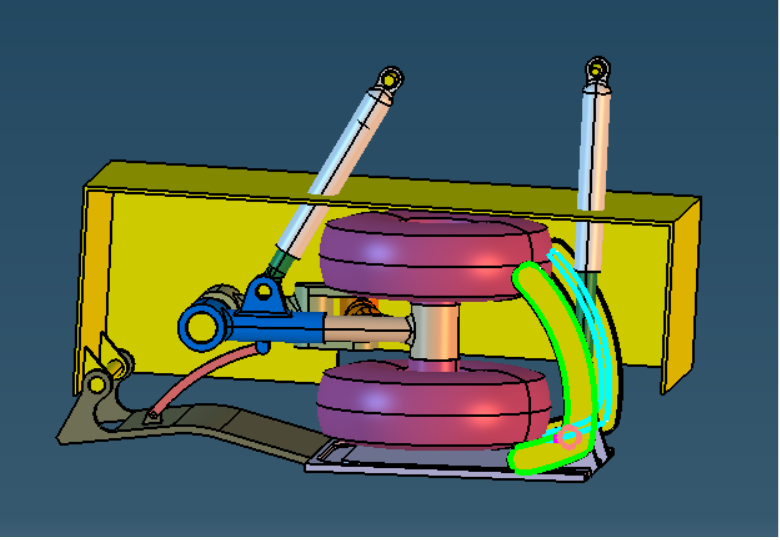
